
Prolonged exposure to particles of crystalline silica can lead to serious and fatal illnesses. Examples include chronic silicosis, interstitial lung disease, and even cancer. People who work in mining, steel, glass, and construction industries are more prone to silica-induced diseases.
It’s essential for these industries to hold safety meetings to discuss how workers can protect themselves from silica dust.
Some common materials that contain silica are:
- Cement and mortar
- Abrasives used for blasting
- Tiles and masonry
- Sand and granite
Whether it’s silica dust or anything else that employees are being overexposed to, you want to apply the control measures to solve the problem.
Isolation
- Enclose the work so all dust is contained within the enclosure and all employees are outside.
- Establish a perimeter around the source of the airborne dust to keep employees away and prevent exposures.
In both cases, careful attention is needed where employees need to enter the affected area once the process has stopped or the enclosure has been removed. There may be considerable dust contamination that can easily become airborne due to traffic and other activities, such as clean up.
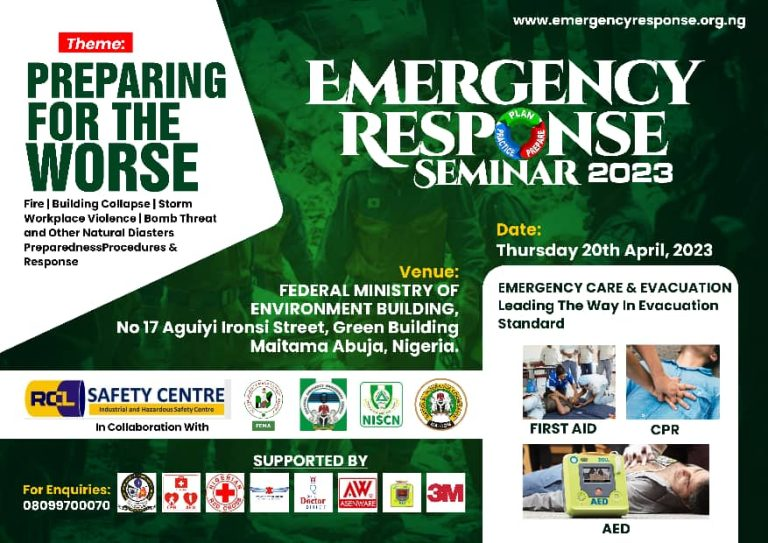
Ventilation
Use a local exhaust or vacuum tool system that removes airborne dust before it gets to the breathing zone of the operator or surrounding employees.
Some important things to watch out for:
- The exhaust system needs to be properly designed in order for it to effectively control exposure. This means an exhaust hood design that allows for effective capture of airborne dust.
- The users need to make sure it is consistently set up according to the manufacturer’s specifications, and remains so throughout its use. This includes using the shortest flexible ducting with the least amount of bends.
- The system needs to be maintained to ensure optimal air exhaust. This includes ensuring the dust collectors are serviced as needed. NOTE: Maintenance of the system can result in significant dust exposures, so respiratory protection may be needed.
- User training on the proper use and maintenance of the equipment.

Wet-Cutting
Use a wet-cutting system that minimizes the generation of dry dust.
What to watch out for:
- Systems meeting Nationally Recognized Testing Lab (NRTL) approval requirements for electrical systems in wet conditions, including GFCI-protected electrical sources.
- Set up and maintenance of the equipment according to the manufacturer’s instructions. This will include ensuring water flow rates within specifications.
- User training on the proper use and maintenance of the equipment.
Work Practice Controls
DO’s
- Work with materials in a way that minimizes the generation of airborne dust.
- Wet sweeping where possible using water or a sweeping compound.
- Use vacuums and exhaust systems with adequate filtration. Reference Section 1532.3
- Wet materials before disturbing, unless that creates significant muscular skeletal strain, slip or other safety hazards.
- Use a water mist to keep airborne dust down.
DON’Ts
- Work with materials dry unless you also have a good exhaust system or there is simply no other way to do it safely, in which case a good respirator protection program will be necessary.
- Use compressed air to clean dust off of surfaces, equipment or yourself.
Respirator Protection
If your employees are using one, then make sure that they are doing so via a respirator protection program that meets Section 5144 requirements, including:
- They are using the right one for the type of material in question. This means:
- The filter will filter out the particle size employees are being exposed to, as well as any other hazardous materials, such as solvents, that may be present.
- The respirator’s protection factor is suitable for the exposures being encountered.
- They are medically approved to wear one.
- It fits them properly. This means the user needs to
- Do a positive/negative fit check every time they put a respirator on.
- Undergo a qualitative or quantitative fit-test at least annually.
- They’ve been trained on the respirators’ limitations and how to properly use, clean and store it.
- This includes making sure they do not have facial hair that breaks or interferes with the seal between the respirator and their face.
- Someone in the organization has been given the responsibility to make sure the program is being implemented correctly.
You can get more training from RCL Safety Centre thru https: www.safetycentre.ng/training_register
At RCL Safety Centre this training is also available in different Nigerian languages like PIDGIN,YORUBA,HAUSA AND IGBO
Our company (RCL Safety Centre) is an indigenous company dedicated to Health, Safety and Environment Training and Services.
We are technical partners of the National Industrial Safety Council of Nigeria (NISCN) as well as approved training partners of most major International Occupational Safety and Health organizations like NEBOSH, and corporate members of ISPON (Institute of Safety Professionals of Nigeria) with thousands of personnel trained in various areas till date.
For more information visit our website: www.safetycentre.ng
Email: sale@safetycentre.ng or mma@safetycentre.ng
Contact us on: 08099700070, 09057666623 or 08164363532